Engineered Solutions
Gravity Roller Conveyors
Gravity roller conveyors are some of the most commonly used types of conveyors in factories and other industrial settings. They offer a simple, reliable, and inexpensive solution to transporting parts, products, and packages. While a conveyor roller may not be the ideal solution for every application, there are many situations that can benefit from the integration of these conveyors.
At Dorner, we offer custom conveyor solutions to help you optimize your production line at every step of the process. Whether you require a gravity roller conveyor, a powered belt conveyor, or a custom configured system with a variety of integrated conveyors, we can help.
How Gravity Conveyors Work
A gravity conveyor moves product by taking advantage of the natural force of gravity. The product sits on rollers that are mounted on a slight decline in order to use gravity to assist forward motion and minimize any frictional resistance. This system uses less energy than other types of conveyors, making it an ideal choice for certain labor-intensive applications.
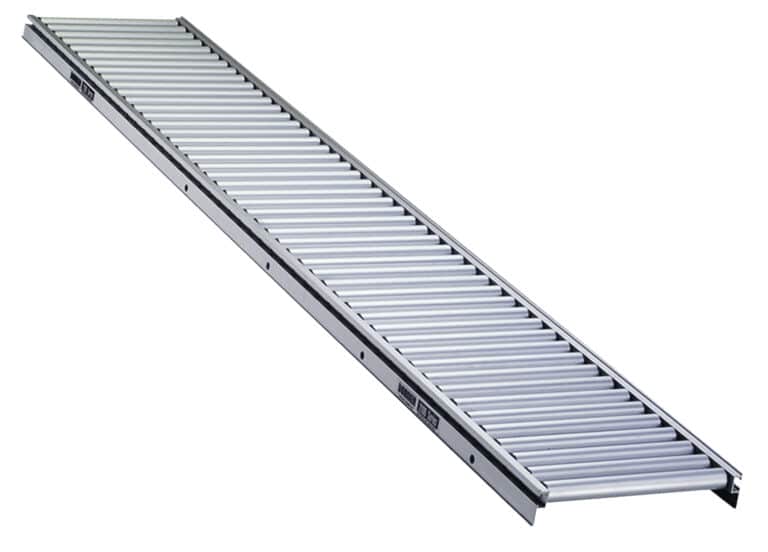
When to Use A Roller Conveyor in Your Production Line
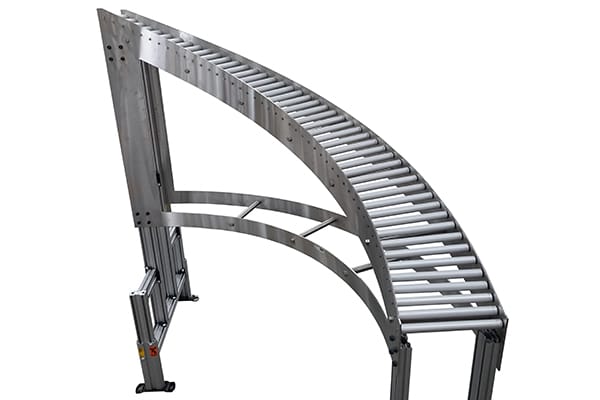
While powered conveyors offer exceptional versatility, speed, and precision, there are a number of applications that benefit from the use of high quality gravity conveyors. In fact, many factories and warehouses, as well as other facilities, are known to use roller conveyors in their assembly or packaging processes.
When it comes to deciding whether to integrate a roller conveyor, the following situations are common reasons for integrating this simple solution.
Your Process Requires A Lot of Human Interaction
With a lower amount of friction than belted conveyors, a roller conveyor is suitable for processes that require operators to shift, rotate, and position product while in motion. Because gravity conveyors are limited in how fast they can move products, operators will have an easier time consistently interacting with the items being conveyed, reducing the need to halt or delay the operation.
You’re Moving Finished or Packaged Products
Gravity roller conveyors offer a simple, efficient solution for getting products from one point to another without the risk of damaging items that may have already been through your production process. If your goal is to transport finished items or packages, a roller conveyor can help you quickly convey your product in an energy-efficient manner.
You Need an Economical Solution
One of the main reasons to consider a gravity conveyor is the cost savings associated with this type of system. When compared to other types of conveyors, such as powered roller or belt conveyors, a gravity conveyor can be a more economical solution, especially for shorter runs and turns. In addition, because there are no moving parts or motors, maintenance costs are typically lower.
Naturally, the number of beneficial applications of a gravity conveyor are lower than those of a powered conveyor, so you likely cannot use roller conveyors for every part of your process. Still, finding areas that would benefit from these conveyors may be a worthwhile way to reduce costs and still maintain high levels of efficiency and productivity.
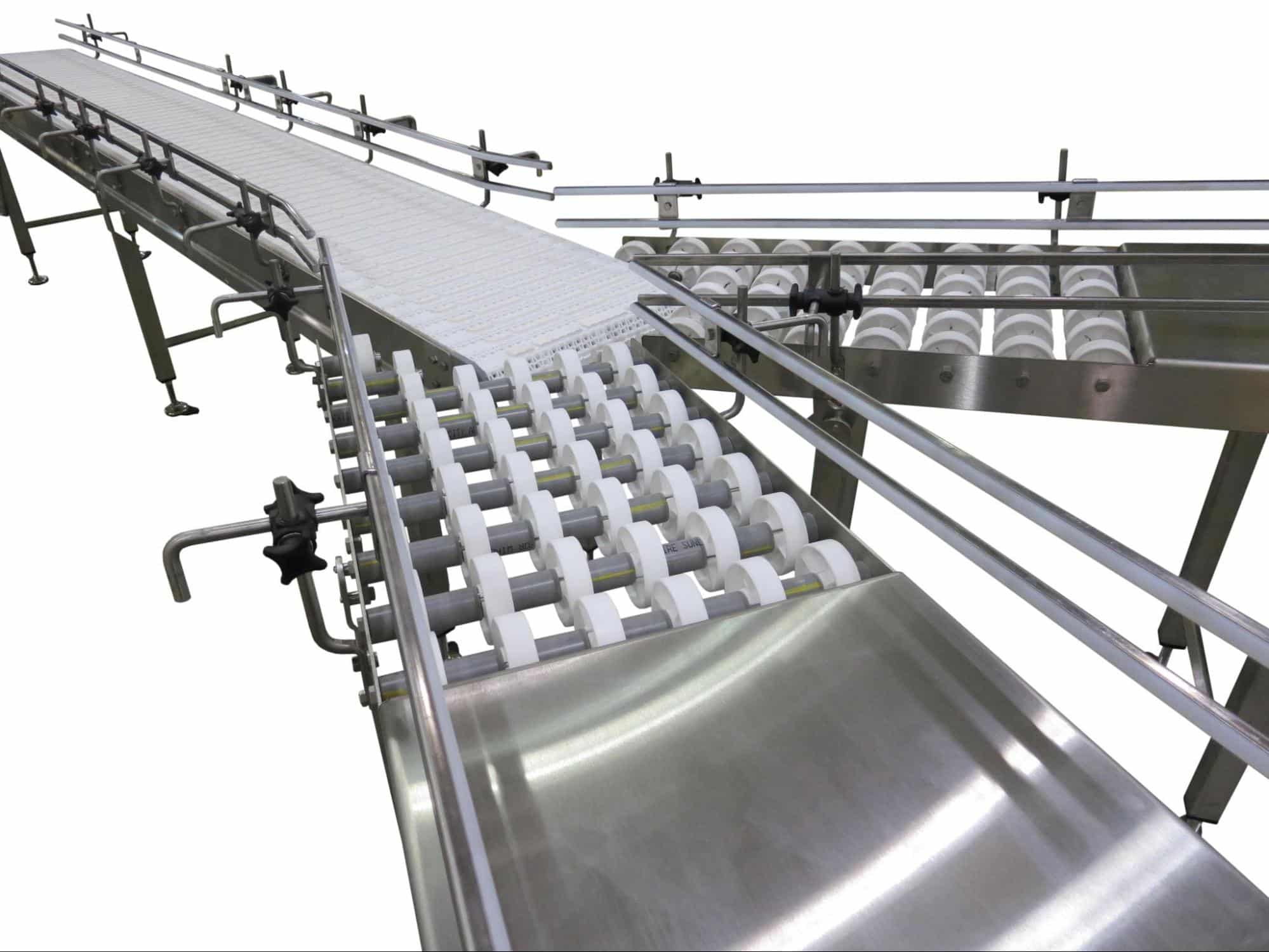
Applications that Benefit From the Use of a Gravity Roller Conveyor
Accumulation
When you need to accumulate product on the conveyor before being moved to the next stage of production, a gravity roller conveyor can be an ideal solution. Accumulation is commonly required for quality control and inspection processes, and a gravity conveyor can provide a simple, efficient means of gathering like product for the completion of those tasks.
Sortation
Picking & Packing
Picking and packing processes often require the movement of product in small increments, which can be easily accomplished with a gravity roller conveyor. Additionally, because these conveyors are typically used in lower-speed applications, it can be easier for operators to keep up with product flow.
Palletizing
Heavy-Duty Conveying
In some cases, a gravity roller conveyor may be the best option for conveying heavy items or items that are difficult to move with other types of conveyors. The 2200 gravity conveyor can withstand loads of up to 80 lbs/ft, making them a versatile and durable solution for many conveying needs.
Material Handling
In many material handling applications, products need to be moved short distances, and a gravity roller conveyor can provide an ideal solution. These conveyors can also be used in conjunction with other types of conveyors, such as belt or chain conveyors, to create a complete system for moving product throughout your facility.
Additional Functionality
In addition to being a simple and efficient way to move product, gravity roller conveyors also offer the opportunity to incorporate additional functionality into your process. For example, you can add pneumatic stops, diverts, or merges to help control the flow of product. You can also install scanners underneath the rollers to capture data about the product as it moves along the conveyor.
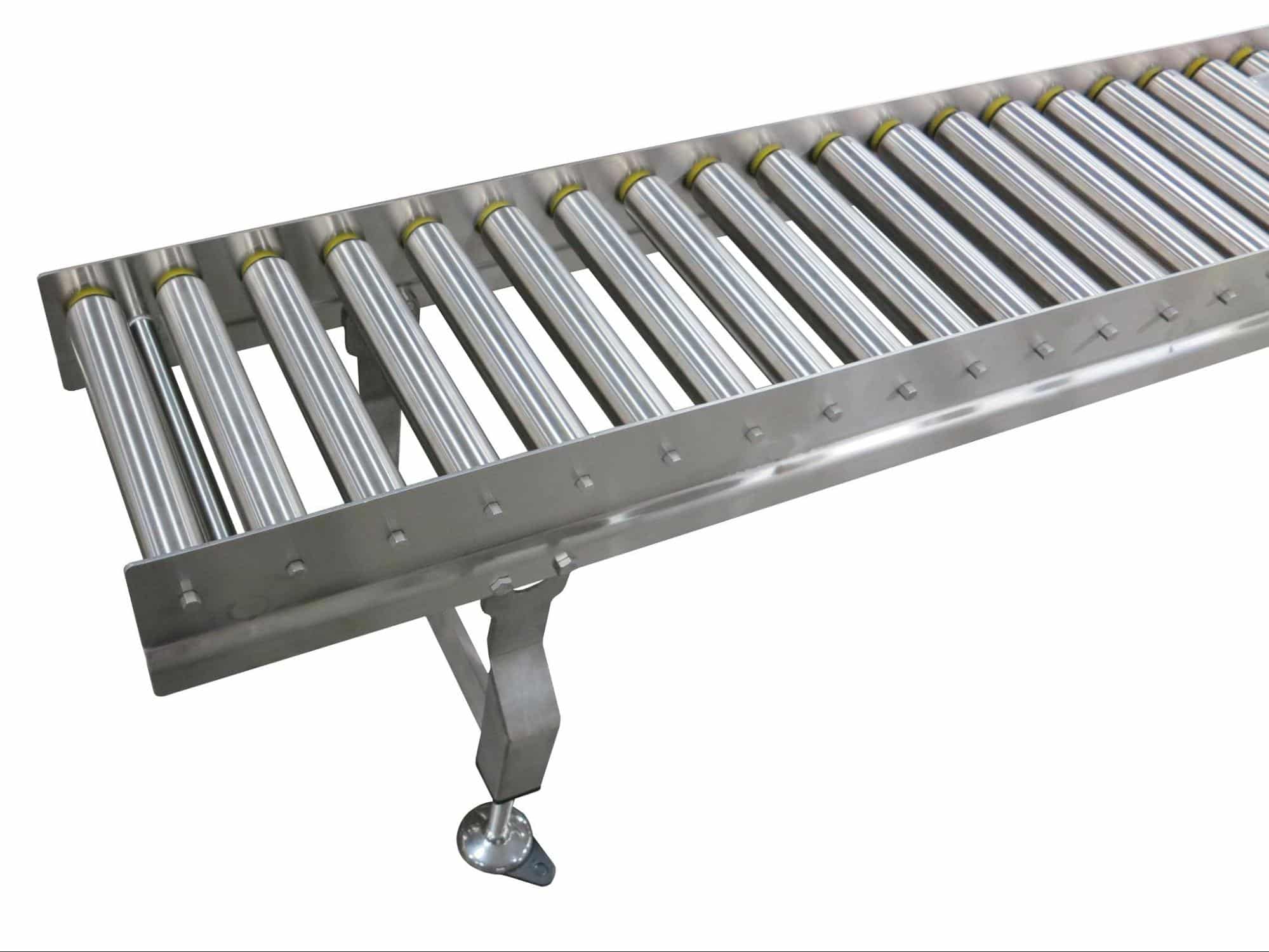
How to Best Integrate Both Conveyor Roller Systems and Powered Conveyors into Your Facility
The best way to integrate both conveyor roller systems and powered conveyors into your facility is to carefully consider the needs of a specific application and then select the type of conveyor that will best meet those needs. In many environments, a combination of conveyor systems will be necessary in order to efficiently and effectively complete essential tasks and processes.
When integrating conveyor systems into your facility, you should:
Consider the Materials, Parts, and Products You’re Moving
Identify the Needs of Your Production Line
Throughout your production line, each part of your process is likely to have different needs. Some processes may require speed and precision while others may utilize more human interaction and require flexibility. Identifying the needs of your production line will help you to choose the right type of conveyor system for each task.
If you need to move product quickly and with precise positioning, for example, a powered conveyor system may be the best option. However, if speed is not as much of a concern, a flexible gravity roller conveyor may be a more cost-effective solution.
Determine Suitable Applications for Each Conveyance System
Powered and roller conveyors are suitable for a number of different applications, and while there may be some overlap, it is crucial to identify which applications are most compatible with the specifics of your operation.
For example, if you are accumulating finished products or packages to be palletized, a pallet gravity conveyor may be a cost-effective and efficient means of moving those items. If you need to inspect a product while it is in motion on a conveyor, a powered belt may be a more suitable option so that you can better manage its speed.
Not sure which conveyor system is right for your needs? Our team can help you find the best solution for your unique applications.
Ensure Conveyors Are Compatible
Dorner’s wide variety of conveyor systems are designed to be easily integrated together in order to create a complete conveying solution for your facility. Our conveyors are compatible with each other and can be seamlessly integrated to create a custom solution that meets the specific needs of your application.
We can help you customize your conveyor system to suit a variety of applications and processes, enhancing your operation to best meet your needs and ensure higher levels of productivity and efficiency. Whether you require powered conveyors, roller belt conveyors, or a combination of both, our team can help you identify the most effective way to configure your conveyor system.
Gravity Conveyors and Other Material Handling Solutions from Dorner
2200 Roller Conveyor
Select one of these conveyor gravity rollers for a range of applications and environments with customizable widths (up to 24”), lengths (up to 12’), and more. Incorporate accessories like fixed end stops, guides and wipers, and motion control to satisfy the needs of your operation with our cost-effective 2200 Series roller conveyor system.
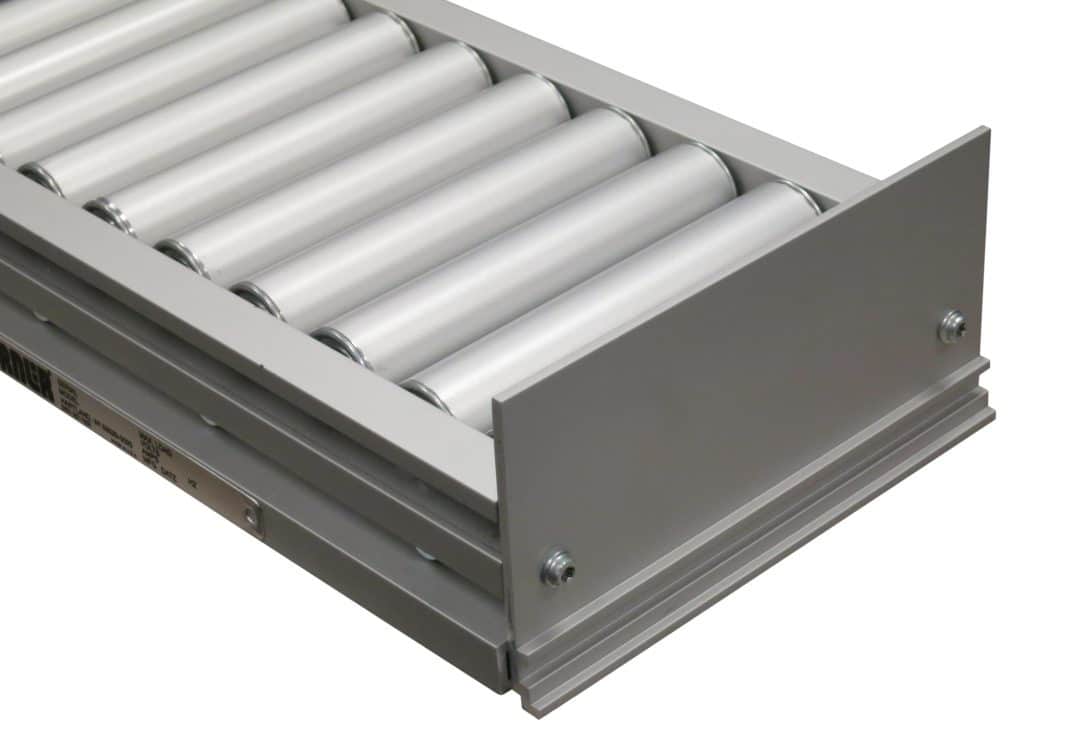
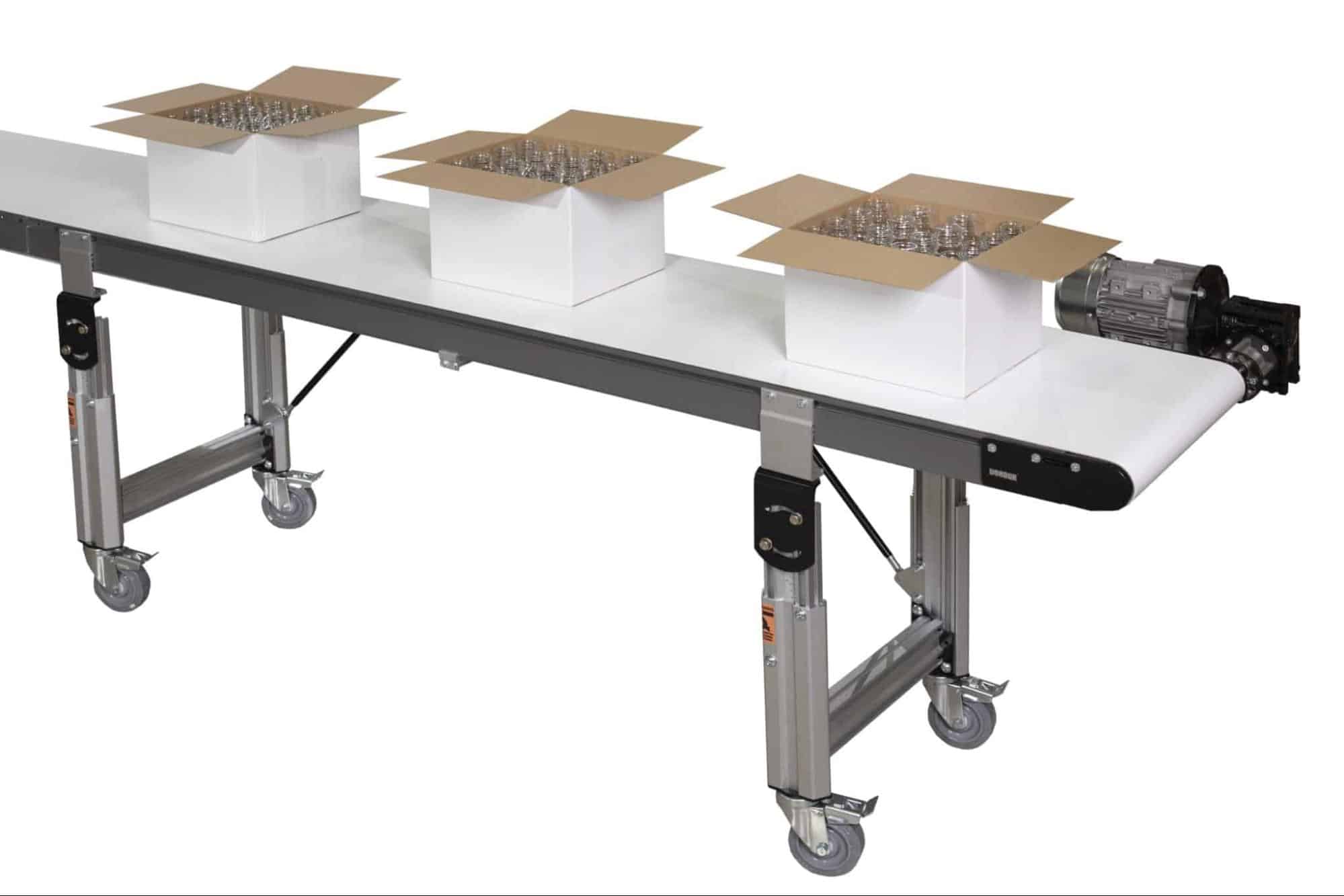
2700 Medium-Duty Conveyor
Ideal for a range of material handling and e-commerce applications, our new 2700 medium-duty conveyor is a low-profile option with a lightweight construction and wider maximum width designed to withstand higher payloads (up to 150 lbs).
Suitable for precise conveying with precision belt tracking and v-guiding, the 2700 medium-duty conveyor is a flexible solution with a minimal footprint for a variety of material handling applications.
DCMove Conveyor
With precision conveyance functionality and a wide load capacity range, the new DCMove conveyor is perfect for a number of industrial applications including packaging, palletizing, and material handling. This easy-to-integrate, economical conveyor has a reduced footprint to help you save space.
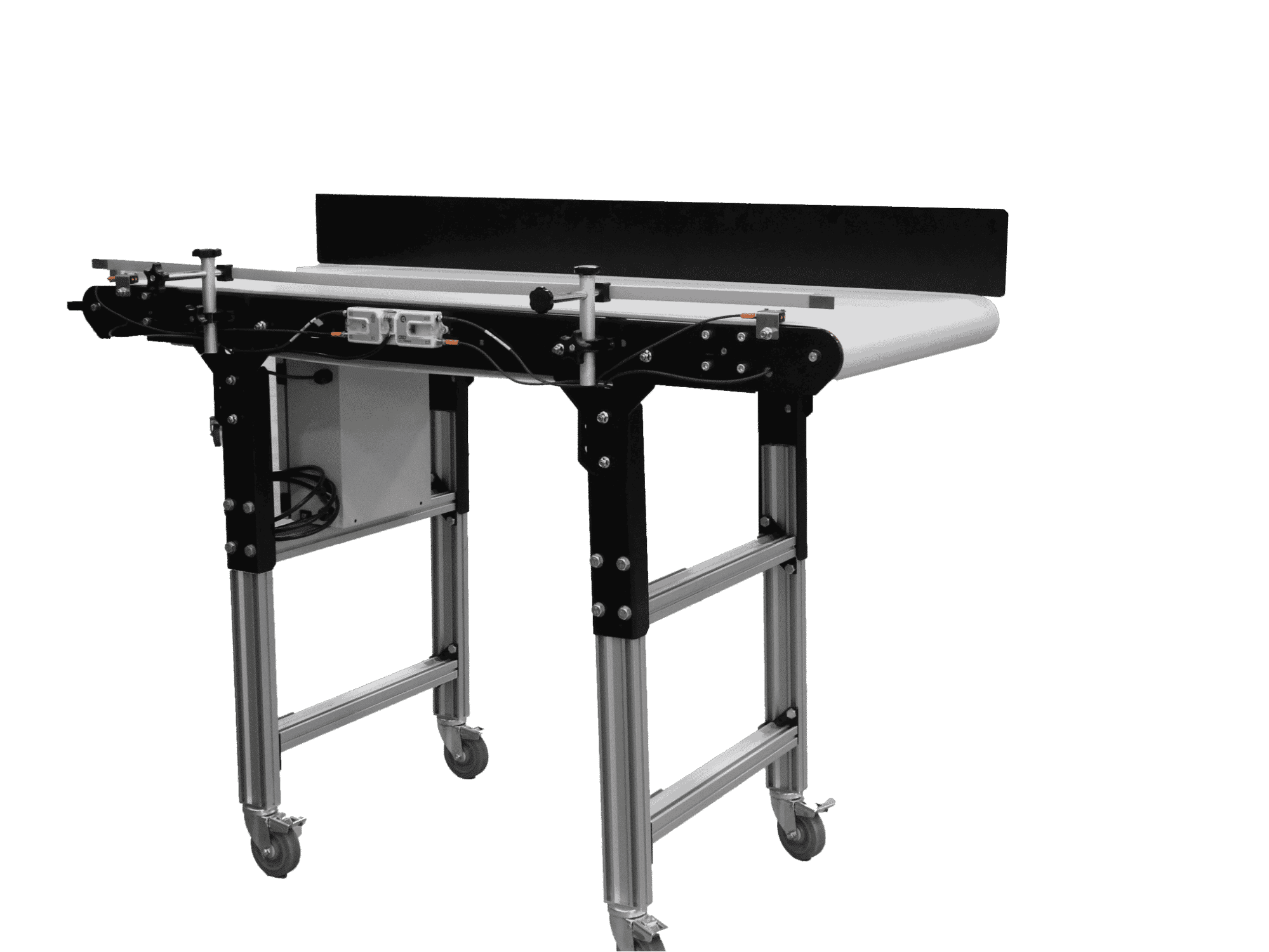
FAQ About Roller Conveyor Systems
A gravity conveyor is a type of conveyor that uses gravity to move materials from one point to another. Gravity conveyors can be used to transport a variety of products, including packages, boxes, and loose materials. These types of conveyors are often used in warehouse and storage applications, though they can be productively integrated in other settings, as well.
Gravity conveyors rely on gravity to move materials, while powered conveyors use an electric motor to move a chain, fabric, or rubber belt to transport materials.
There are a few different ways to keep pallets in place on gravity roller conveyors. One option is to use side rails, which can be placed on either side of the conveyor to keep pallets from shifting. Another option is to use load stop devices, which can be attached to the conveyor frame to prevent pallets from rolling off the conveyor.
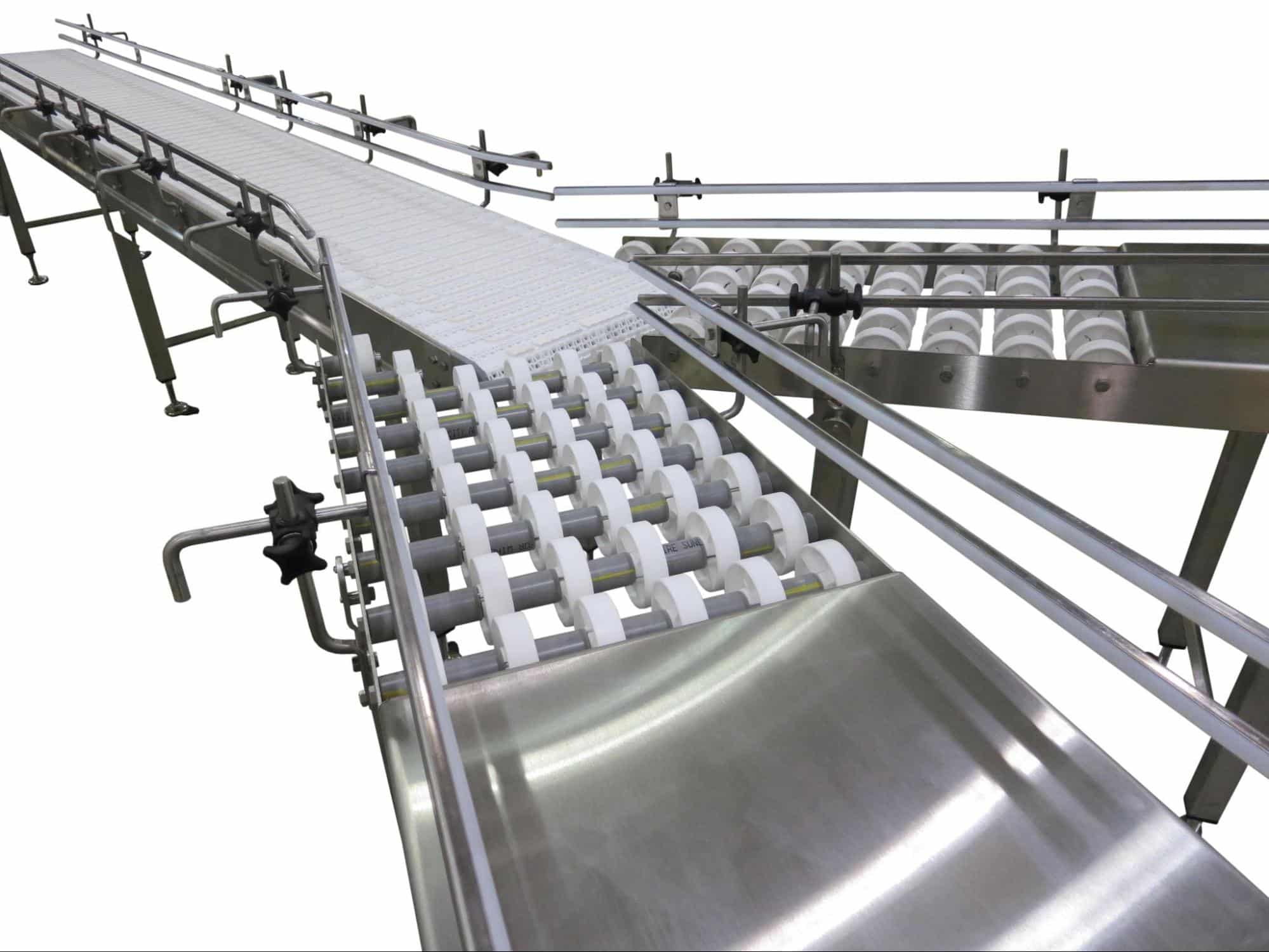
Get a Custom Conveying Solution With Powered and Gravity Conveyors With Dorner
Integrating Dorner conveyor systems with powered and gravity conveyors can provide a number of benefits for your business. Our team can help you select the right type of conveyor system for your needs and configure it to work seamlessly with your existing equipment. We also offer a wide range of accessories, including load stop devices, side rails, and more, to ensure that your conveying solution is tailored to your specific requirements.
Get in touch with our team to learn more about how our integrated conveying solutions can improve the efficiency and productivity of your operation.